Exploring Pressure Dynamics in Rough-Surfaced U-Bend Pipelines: A Comparative Study of Water and Nanofluid Composites across Varying Mass Flow Rates
DOI:
https://doi.org/10.37934/sijn.3.1.121bKeywords:
Fluid dynamics, U-bend pipes, rough walls, computational fluid dynamics, ansys fluent, pressure characteristics, nanofluids, water/Al₂O₃ mixture, water/ZnO mixture, mass flow rateAbstract
This study investigates fluid flow in U-bend pipes with rough walls, an essential aspect of fluid engineering to improve system efficiency in applications such as heat exchangers and industrial piping. It compares numerical calculation results with Computational Fluid Dynamics (CFD) simulations performed in Ansys Fluent for three types of fluids: water, nano-Al₂O₃ (Water/Al₂O₃), and nano-ZnO (Water/ZnO), at mass flow rates of 0.74 kg/s, 0.75 kg/s, and 0.76 kg/s. These findings are validated against a reference value of 0.735 kg/s from Ansys. The results indicate an increase in total pressure with rising mass flow rates: water achieved the highest total pressure, ranging from 2132.72 Pa (at 0.74 kg/s) to 2252.316 Pa (at 0.76 kg/s), followed by Water/Al₂O₃, with pressures from 2100.92 Pa to 2220.59 Pa, and Water/ZnO, which had the lowest pressures ranging from 2091.69 Pa to 2208.73 Pa. ANOVA analysis reveals a significant impact of both fluid type and mass flow rate on total pressure, along with a significant interaction between the two factors. This underscores the importance of selecting appropriate combinations of fluid type and flow rate for optimal efficiency and reliability in industrial system design.
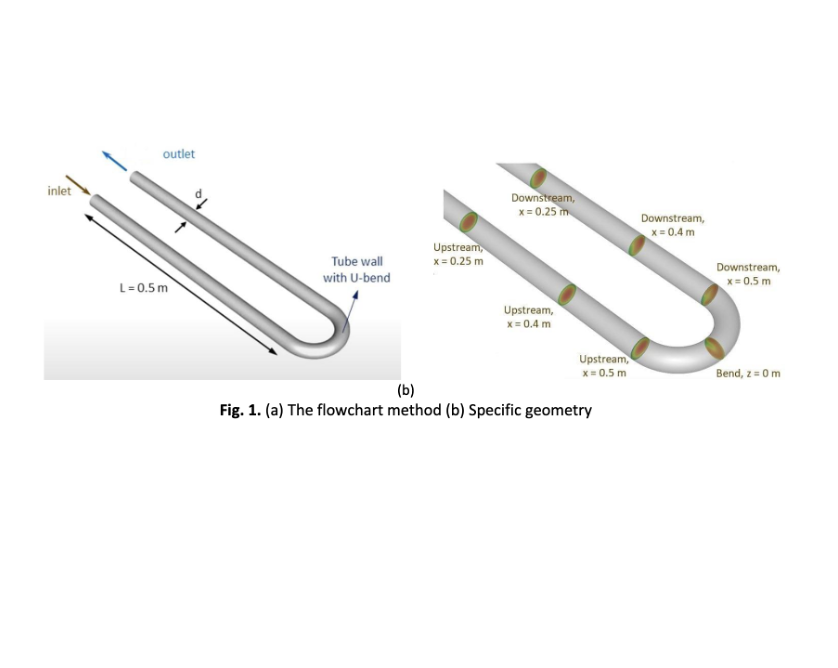