Mechanical Properties of Friction Stir Welding Assisted Cooling
DOI:
https://doi.org/10.37934/sijmpe.3.1.118Keywords:
FSW, AA6061, assisted cooling, MQL, machine coolant, mechanical propertiesAbstract
Friction Stir Welding (FSW) is a solid-state joining technique widely used for aluminium alloys due to its ability to produce high-quality welds without melting the base material. However, excessive heat generation during the process can deteriorate the microstructure, leading to reduced mechanical properties. Despite various advancements, limited research has focused on optimizing cooling strategies to enhance weld strength and quality. Therefore, this study addresses this gap by investigating the effects of assisted cooling on the mechanical properties of FSW joints using the Taguchi optimization method to identify the optimal welding parameters. A series of nine experiments were conducted on AA6061 aluminium alloy, varying tool rotation speeds between 900rpm to 1400 rpm, different coolant compositions, and varied coolant flow rates between 10 mL/min to 30 mL/min. The axial force and travel speed are constant at 5 kN and 108 mm/min respectively. The results demonstrated that assisted cooling significantly influenced the weld quality. The highest tensile strength was recorded at a tool rotation speed of 1150 rpm with a coolant flow rate of 30 mL/min, showing a 19.53% improvement over the Parent material without cooling. Hardness measurements indicated that welds produced under assisted cooling exhibited higher microhardness values in the weld zone, particularly at a 1:1 coolant-water mixture with a 30 mL/min flow rate. From the study that we found using machine coolant during welding assisted cooling, its mange to increase 24% in joint strength from the parent material. These findings highlight the critical role of cooling in enhancing FSW joint properties and provide valuable insights into optimizing process parameters for industrial applications. By mitigating heat-related issues, this study contributes to the advancement of FSW technology, promoting its adoption in sectors requiring high-strength aluminium welds, such as aerospace, automotive, and marine industries.
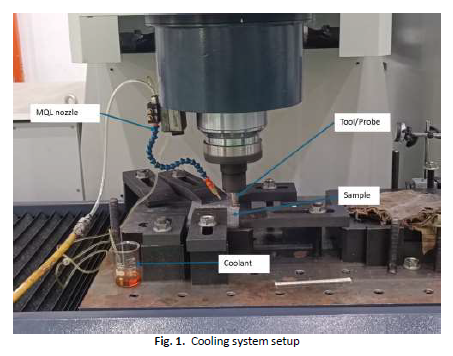