Finite Element Analysis and Optimization for Structure of Dry Ice Cleaning Machine Frame
DOI:
https://doi.org/10.37934/sijmpe.2.1.1123aKeywords:
Dry ice cleaning, finite element analysis, response surface optimization, modal analysisAbstract
This study aims to optimize the design of a dry ice cleaning machine frame. According to the typical working condition data of the dry ice cleaning machine, the Finite Element Analysis (FEA) was used for static structural analysis. It is found that the U-shaped tube is the most easily damaged component. The Response Surface Optimization (RSO) method was used in this study to optimize the parameters of the U-shaped tube size. Here, the maximum total deformation is reduced from 0.058 to 0.022 compared to the original design, and the mass is increased by 2.43kg. Subsequently, the modal analysis of the optimized dry ice cleaning machine frame was carried out to determine the first 6 natural frequencies and vibration modes. The results show that the optimization design of the dry ice cleaning machine frame effectively improves the working reliability of key components, and the overall frame is also in a safe state. This study provides theoretical and practical guidance for the design and improvement of dry ice cleaning machines.
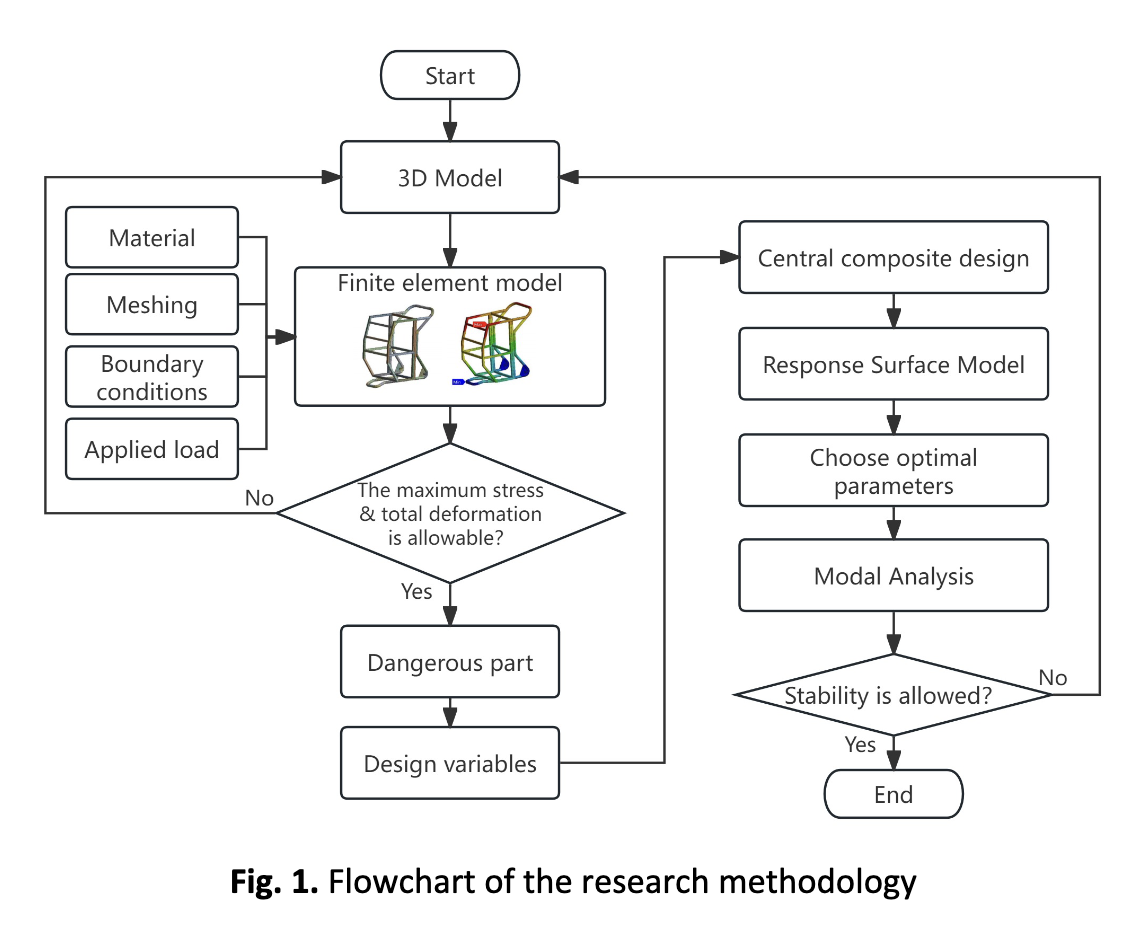